Request a qoute.
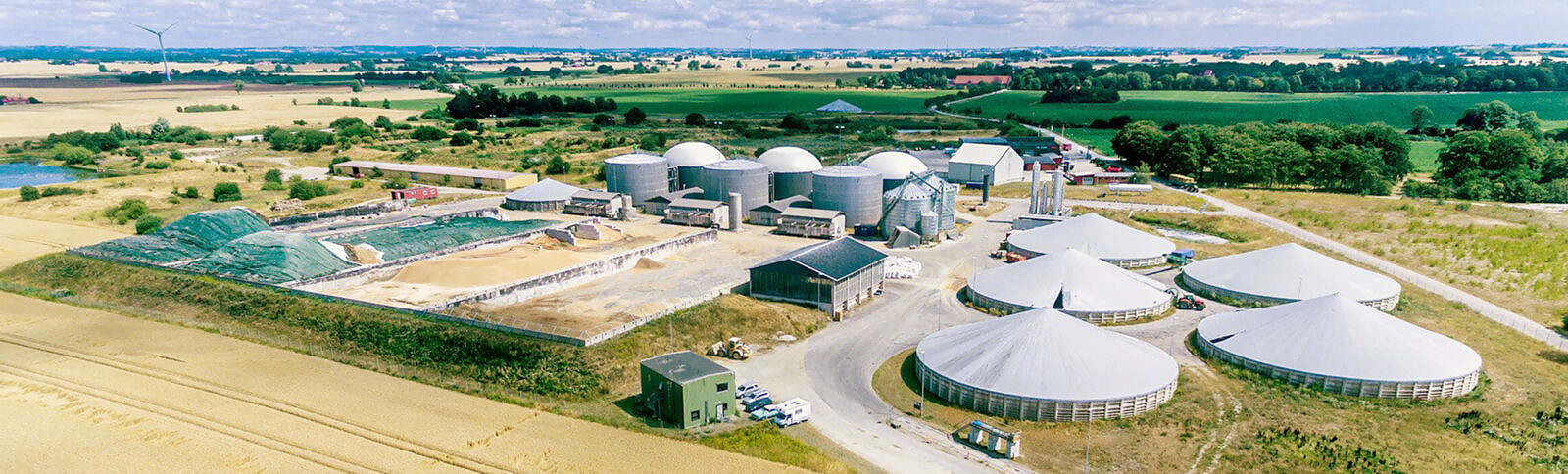
Replacing tradition with innovation in the biogas industry – creating sustainable business value
The process of biogas production is a series of complex and costly stages aimed at effectively producing methane from waste. Traditional biogas plants extensively utilize a wide range of waste materials such as feedstock, which includes biomass, among other types of waste. Since feedstock is renewable, biogas plants produce green energy, contributing to a circular economy. According to the World Bioenergy Association, the sector of biogas production is one of the fastest-growing among all biofuel sectors.
There are several parts of a biogas production process that can benefit from a cost-efficient ozone treatment solution like the ones we offer. Although there are many possibilities, we have identified three main treatment applications in biogas plants that once managed properly can create real business value:
- Substrate pre-treatment to enhance the total biogas yield
- H2S reduction for methane upgrading
- Odor control, preventing serious consequences
It is interesting to know that the average growth of biogas production was 11.2% in 2014, reaching an overall production of 58.7 billion Nm3. Almost half of this amount was produced in Europe where over 17 000 biogas plants are in operation. Germany is the leading country in terms of number of biogas plants, with a total of 11 000 installations, followed by Italy with 1 600 and France with 800.
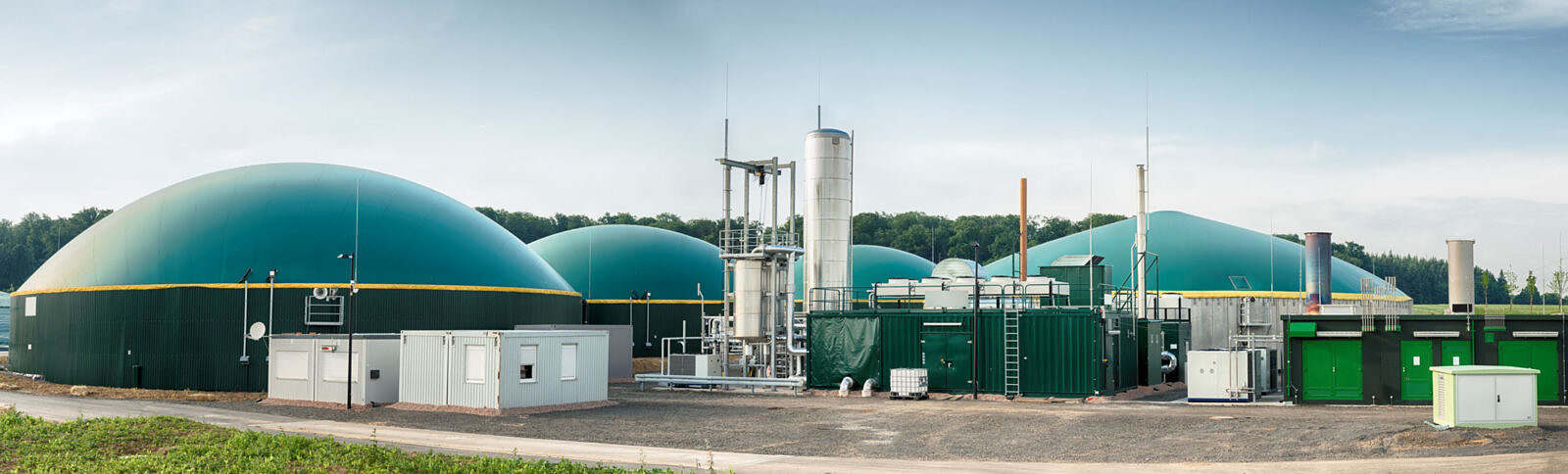
Common challenges facing the Biogas industry.
Sulfur is the issue
At each stage of the biogas production process, sulfur compounds and ions are commonly present. These compounds are often responsible for a variety of issues affecting the overall performance. For instance, high amounts of sulfur ions in the feedstock enhance the activity of sulfur-reducing bacteria (SRB) in the digester, inhibiting the activity of methane-producing microorganisms such as archaea.
As a result, the yield of methane production is reduced while the production of reduced-sulfur compounds, such as H2S, is favored. When high concentrations of H2S are released from the digester, the process may cause odor and corrosion problems. In particular, odor problems are common in biogas plants, since H2S has one of the lowest odor thresholds known, making the human nose very sensitive even to trace concentrations.
Feedstock pretreatment
Prior to the anaerobic digestion stage, a pretreatment step is often implemented. The purpose of this step is to reduce the workload of the hydrolytic fermentative bacteria by making the substrate more easily biodegradable. This includes properties such as increasing the surface area, dissolving complex matter, and reducing crystallinity in the most common polymers such as cellulose etc.
The most common types of pretreatment applied today are summarized in the tables below.
Pre-treatments prior to anaerobic digestion
Physical pretreatments | |
Mechanical | Milling to reduce particle size, increasing the biomass availability. |
Thermal | Heating (200ºC), disrupting hydrogen bonds (chemical macrostructures), increasing biomass availability. Leads to a high energy demand. |
Chemical pretreatments | |
Alkali | Alkali treatment over several weeks, easing the degradation of ligno-cellulosic compounds. Requires large amounts of chemicals, chemical handling and leads to a slow process. |
Ozone treatment | Inline ozonation, significantly increasing the biodegradability of stable organic matter, potentially tripling biogas production. |
Biological pretreatments | |
Microbiological | Compostation, an aerobic pretreatment step forming hydrolytic enzymes, facilitating the first step of the anaerobic digestion. |
Fungal | Pure cultures of an aerobic fungi during a four day incubation time can result in up to 40% more biogas produced, and an increase in the grade. |
Anaerobic digestion
After the pretreatment stage, the feedstock enters the digester for biochemical conversion. In this unit, several types of microorganisms react with the feedstock in different stages. All stages are anaerobic i.e. in absence of oxygen. These are summarized in the table below.
The methane production through anaerobic digestion may be performed with a single-stage or two-stage process. In the first case, all the reaction steps above are carried out in the same reactor. The substrate is converted into methane with a concentration of 50-55% in the biogas, depending on the type of substrate. In a two-stage process, only the reaction steps until the acetogenesis are carried out in the first digester.
The following methane production is performed in a second stage, called the methane upgrading stage. By splitting the process into two stages, it is possible to increase the methane concentration in the biogas up to 70%. Therefore, the system becomes more efficient and the costs for the following biogas purification are reduced.
The steps of the anaerobic digestion stage
Step | Description |
---|---|
Hydrolysis | Breaking down large substrates, such as cellulose and proteins to glucose and amino acids |
Fermentation | Formation of volatile organic acids and alcohols |
Acetogenesis | Formation of acetate, carbon dioxide, and hydrogen |
Methanogenesis | Formation of methane and carbon dioxide |
Corrosion and odor build-up in biogas after-treatment
In the biogas after the methane upgrading, high concentrations of hydrogen sulfide are often present, creating issues for the following process steps. Corrosion is one of the issues to be considered, since very high H2S levels may corrode pipes and process instrumentation, resulting in costs up to several thousand euros per year. Odor is also one of the major problems related to the methane upgrading off-gas. This is due to the high sensitivity of the human nose to hydrogen sulfide, since the odor receptors are triggered for concentrations in the part-per-billion (ppb) range.
Thus, even a small leak in the process lines or an opening in a process step may create an odor issue for a large area, since the emitted gas needs to be diluted up to 200 000 times before the odor is masked.
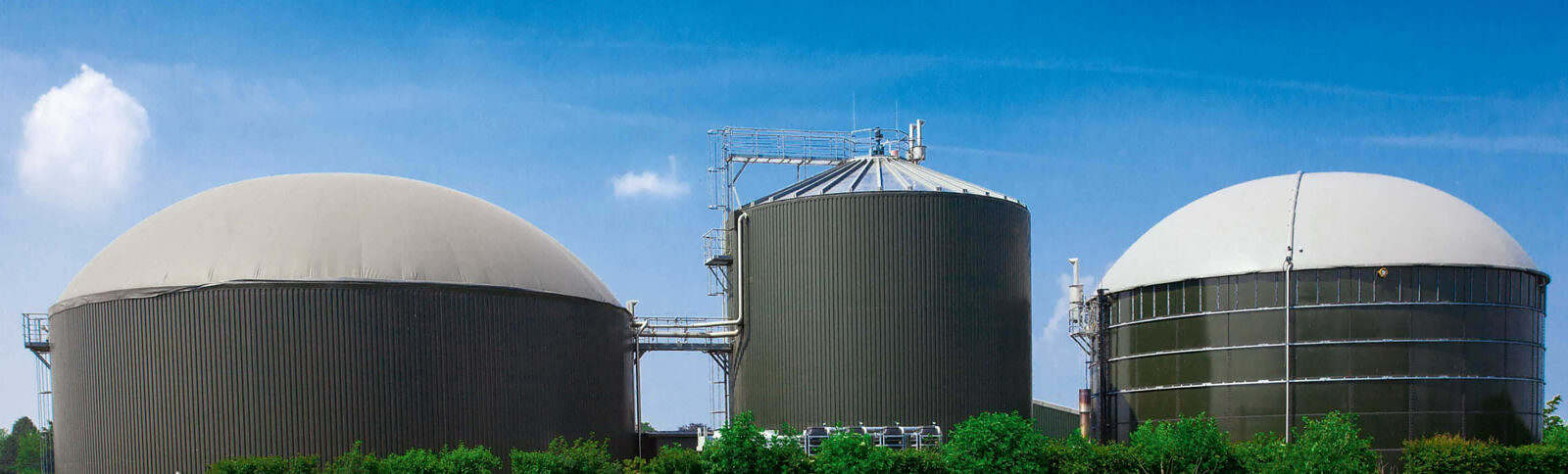
Our solutions for a modern biogas production.
Treating feedstock with ozone for a greater production output
Ozone is known for its highly oxidative properties, and has been shown to be able to degrade parts of the complex organic matter used as feedstock for an anaerobic digester. For example, when applying ozone to a feedstock of waste activated sludge, the effects are multiple. When ozone is properly dosed, the substrate conversion to biogas can be greatly increased, as shown in the figure. In many cases, such as biogas production from waste activated sludge, the results show a strong positive impact of the ozone treatment. This result is due to the high content of aerobic bacteria and non-degraded organic matter in this type of feedstock.
Substrate conversion to biogas

Under these conditions, ozone quickly oxidizes any unsaturated bond, forming radicals, which continue to oxidize other organic matter. This reaction mechanism leads to a higher biodegradability of the feedstock, which is translated to higher biogas production. The increase in biogas production is proportional to the ozone injection in the system. The more ozone is used, the higher the biodegradability and the methane yield. As shown in the study below by Bougrier et. al. at “Laboratoire de Biogechnologie de l’Environnement”, the ozone pretreatment improves the biogas production, with an optimum around 0.15 g O3 per g total solids, resulting in an increase of approx.150% in the biogas production, compared to the untreated feedstock.
Effectivize the process of H2S reduction by ozone treatment in the digester
When the biogas is produced in a two-stage process, it is possible to reduce the H2S concentration before the methane upgrading by injecting ozone in the digester. In this way, the H2S is reduced even before the methane production, resulting in a more efficient system and lower costs for the final biogas cleaning.
Since the digestion process is anaerobic, the ozone injection needs to be carefully controlled to not compromise the process conditions. Normally, the ozone is injected in the air pocket above the bio-bed in the digester unit. Alternatively, it can be injected in an intermediate tank between the digester and the methane upgrading unit.
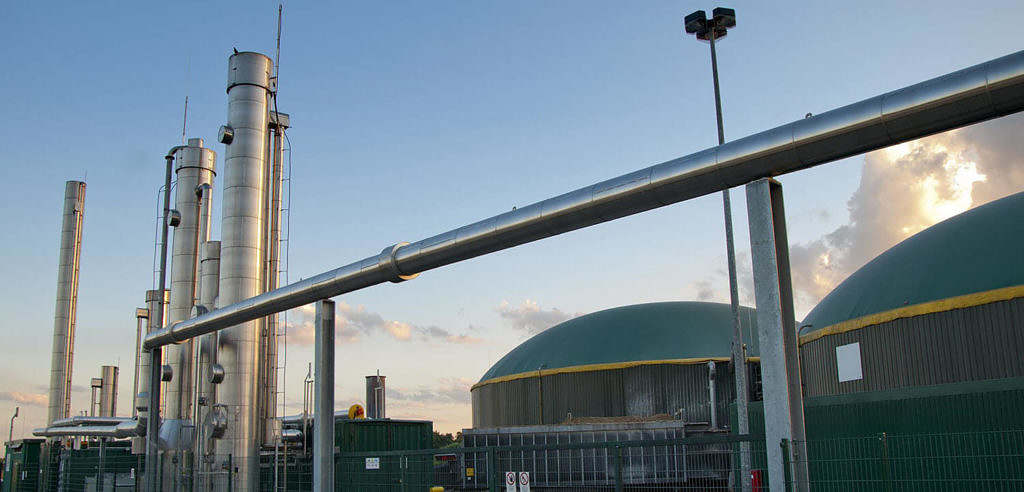
Benefits of odor control with ozone-based solutions
Mellifiq has a long history of developing innovative advanced air treatment solutions for odor emissions. We not only have greatly improved the cost-efficiency of the process of air treatment while keeping the highest industry standards in terms of removal grade, we keep delivering the same great results year after year during our solutions entire lifetime.
In the figure below you can see a simple comparison of operational costs, between an average traditional solution and our solutions. The operating costs of the traditional solution are more than four times higher than those of our combined solutions, even for sub-optimal configurations. Yet the effectiveness of our solutions is at levels higher than 95%, which traditional solutions simply cannot reach.
You will not only increase the efficiency of odor removal in your plant, but you will also lower your operational costs. These are measures that will save you up to 100 000 euros per year, every year. That is sustainable economics. Every year.
The figures below also highlight another unique feature, the flexibility of our solution. Since each biogas process is different and has different requirements, it is important to adjust our system to the needs of each specific plant and the requirements of our customers. Therefore, we carefully design each and every solution, tailoring it for your specific needs, in order to maximize your outcome and benefits while keeping your costs low as shown in the bellow presented case.
Besides the great cost savings, our solution ensures high-efficiency and robust performance throughout its lifetime, resulting in an effective odor removal for a very long time.
Mellifiq’s solutions are not only sustainable, durable and require low maintenance, they also require low energy to operate which minimizes your operation’s environmental impact.
Mellifiq’s solutions for odor control is composed by several stages, including the Ozonetech RENA Pro ozone solution and Nodora advanced air filter systems.
Read more on Odor Control.
Operating costs
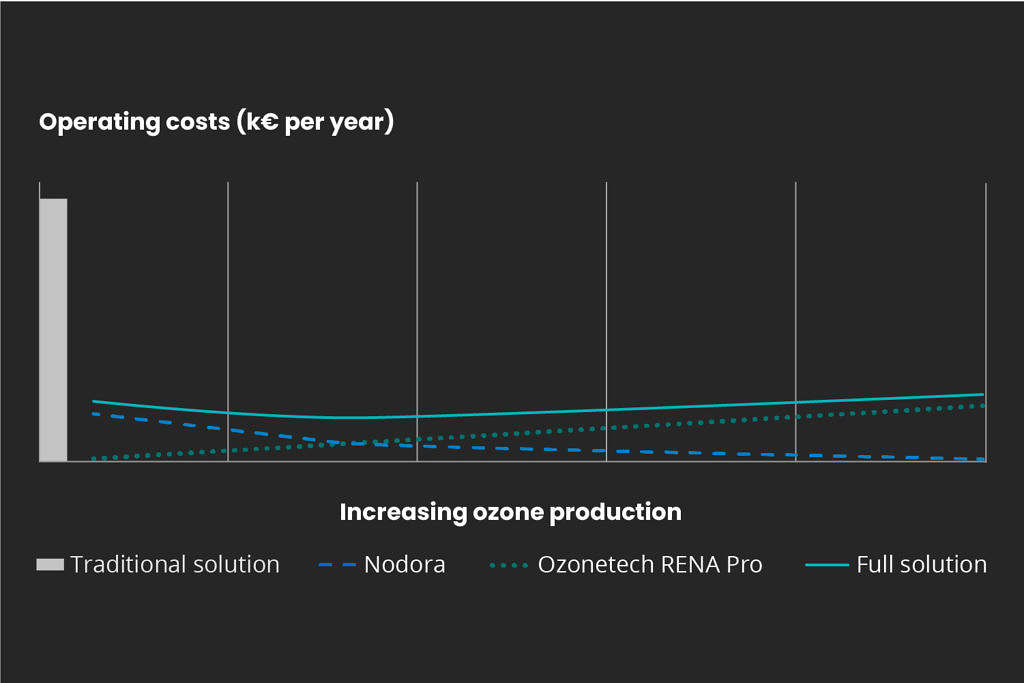
Enabling the reuse of liquid effluent
After the production of biogas, the liquid effluent still has a high content of nitrogenous compounds which constitute an important resource. These can be reused in agriculture as crops fertilizer, thus providing important business value. However, prior to effective reuse, further treatment is needed for removing emitted odors and unpleasant colors.
Our treatment solutions create significant improvement in business profitability and sustainability by solving both problems at once. By injecting ozone in the effluent, the benefits start at the source, minimizing odors even before the emission. In addition, the COD content is greatly reduced, resulting in a color change that enables these effluents to be reused as fertilizers.
Read more about Odor Control and the Ozonetech RENA Pro Solution, for treating odors.
Read more about COD Treatment and the Ozonetech RENA Vivo Solution, for reducing COD.
Green businesses should use green technologies
One of the challenges of biogas plants is the strict requirement of H2S removal after the anaerobic digestion stage, before upgrading.
Another constant source of concern is the odors emitted from the biogas plant. Today, both can be solved effectively, and in a sustainable way.
We have developed a catalyst specifically for H2S removal: the RubicatTM. Even without oxygen, H2S is removed, leaving no traces before the upgrading stage. As the working mechanism is catalytic, the Rubicat has a much longer lifespan compared to traditional technologies, such as activated carbons. The Nodora CAT can yield a 40-95% reduction in operating costs.
In addition, one can handle the odor problems inside the plant using our treatment solutions very cost-effectively on-site. The treatment is applied to the existing ventilation to reduce odorants to then pass through a Nodora ADS as a final polishing stage, before discharge.
Ambitious biogas producers have an additional option: to treat the biomass with ozone, which in some applications can maximize the business value by doubling the amount of biogas yield.
Regardless of application, the treatment will be efficient, green and easy to manage.
Our odor treatment solutions at biogas plants
H2S removal before upgrading
With our advanced air filter solution you don’t need several other add-on technologies to take care of the H2S. No activated carbon, no ozone, or any other treatment method is required. Our unique, in-house developed Nodora CAT advanced air filter, comes equipped with the OCM-Rubicat, a pelletized adsorption compound based on iron hydroxide—hydrogen sulfide and is chemically bound and thus removes gas much more efficient than other adsorption media. The material is continuously regenerated by adding aerial oxygen. This achieves high loading rates of more than 50% by mass based on commercial products.
The Nodora system is on its own sufficient to treat your H2S problems. The Nodora system is in fact one the most efficient advanced air filter systems on the market and is designed to constantly maximize the utilization of the active material, hence highly increasing the H2S removal efficiency and prolonging the lifetime of the filter material.
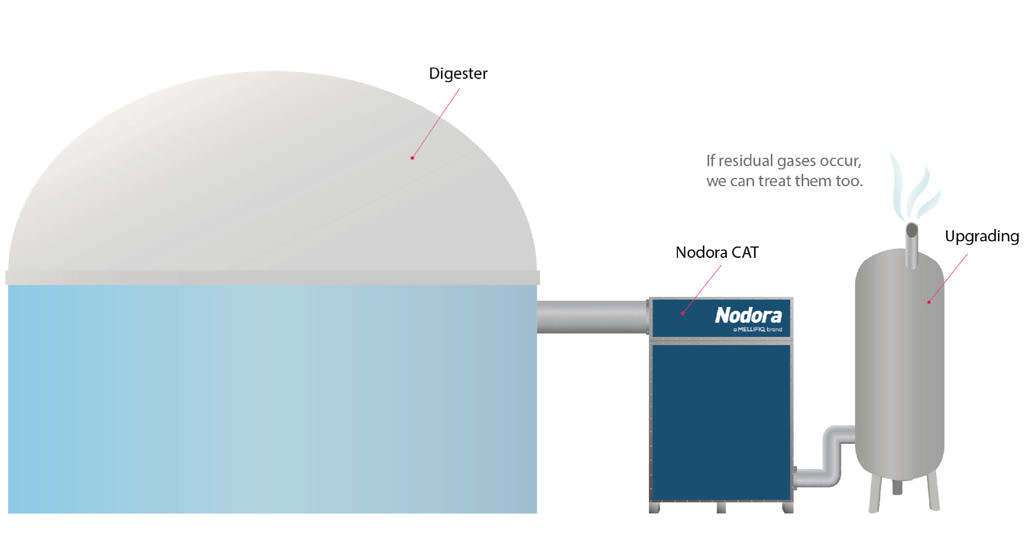
Inhouse odor removal
The odors from inhouse sources are removed through the ventilation and the collected odors can then be treated using Ozonetech RENA Pro and Nodora ADS before the air is discharged into the environment.
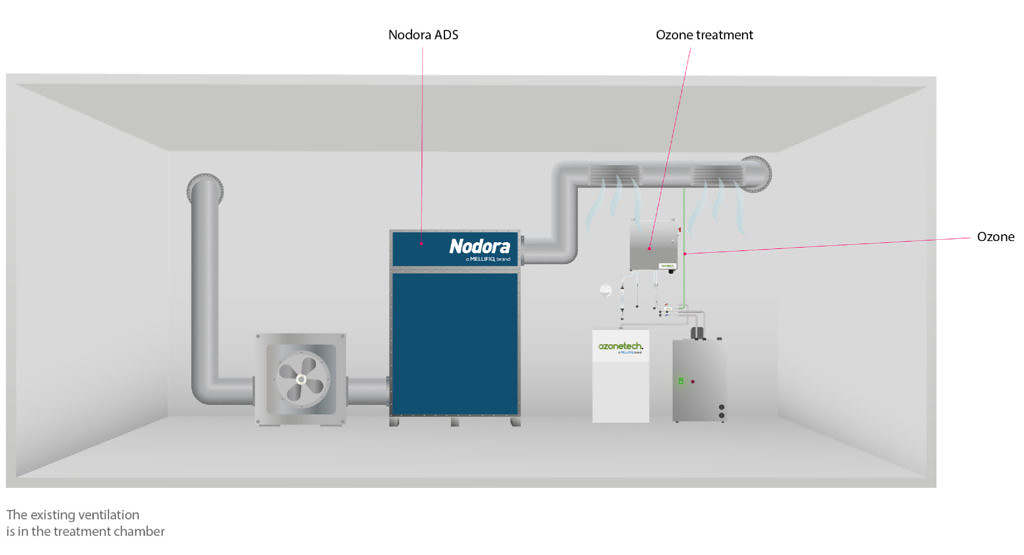
No reconstruction needed. Minimal operating cost.
Our most important advice is to carefully analyze the air. The analyses and pilot tests we perform at our facilities focus on flows and concentrations, preparing the design of the optimal treating method.
Nodora is installed in industries with strong regulatory requirements for odor reduction. All Nodora systems are tailored to the current load to achieve maximum possible H2S and odor reduction. One of many benefits when combining one of our ozone solutions and Nodora is that the active material is active at least five times longer than a solution without prior treatment by our ozone solution.
Removal efficiency over time
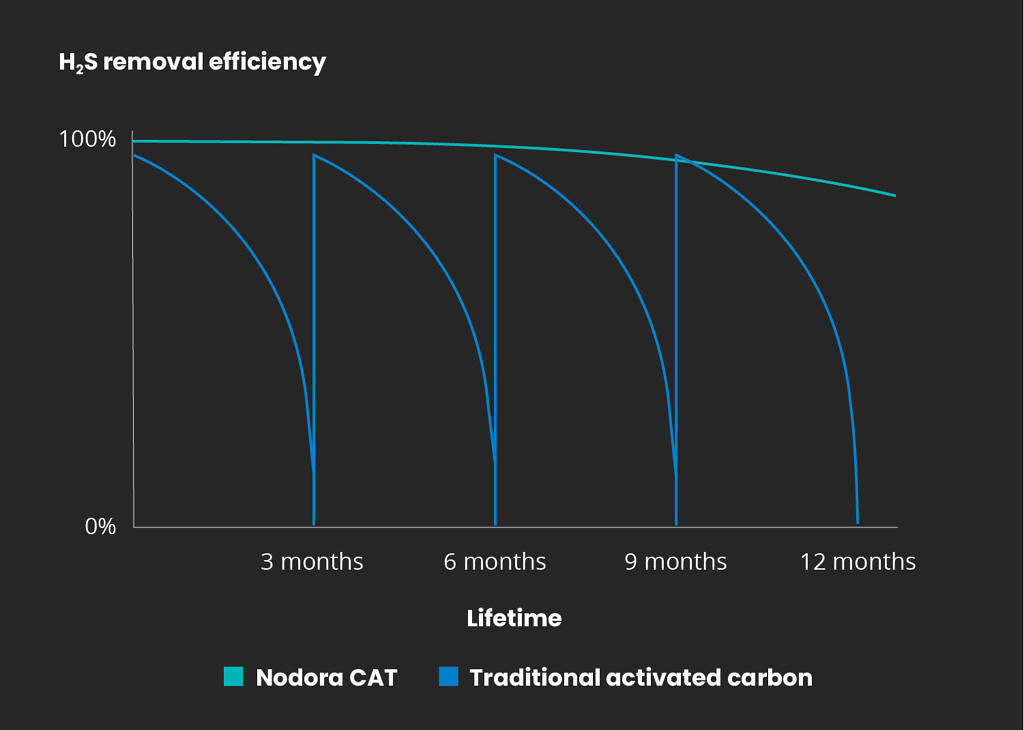
A standard solution using activated carbon treatment is both costly and ineffective compared to our Nodora CAT. The high performance of Nodora CAT is due to the advanced active material used, the material mix and the overall design making use of all filter material equally. The experiments were conducted in Stockholm, with the collaboration of KTH Royal Institute of Technology. Real biogas conditions were tested with an H2S concentration of 1000 ppm.
Estimated annual costs of H2S treatment (EUR)

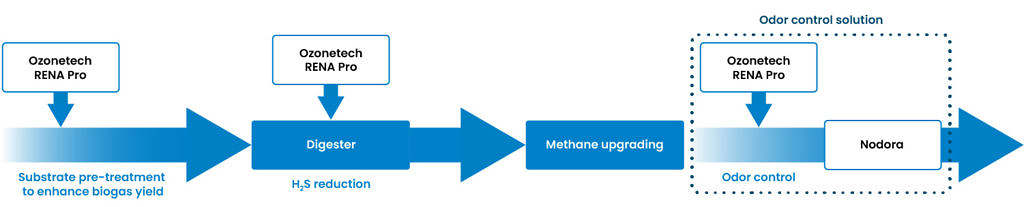
Application | Purpose | Result |
---|---|---|
Substrate pre-treatment to enhance biogas yield | Breaking down large polymers into monomers | Up to 100% higher substrate conversion to biogas |
H2S reduction for methane upgrading | Enable biofuel methane purity through H2S removal | Up to 30% more methane produced |
Odor control | Removal of odorous and corrosive contaminants | Minimized odor and H2S |
Recommended products
Ozonetech RENA Pro Series
The Ozonetech RENA Pro segment offers the following operational enhancements:
- Highly efficient ozone generation reduces energy consumption and footprint
- Stable and reliable ozone production over time
- High-quality fed-gas used (concentrated, dried oxygen from oxygen generator)
- Pure ozone output. No by-products such as NOx, no nitric acid (HNO3) nor salt formation; extending longevity of the system
- Efficient heat management (liquid cooling) for stable and reliable operation, also extending longevity of system
- Minimized maintenance due to clever design; pure, dry oxygen fed-gas and liquid cooling
- Teflon-hose ozone distribution
- Rugged design for harsh environments
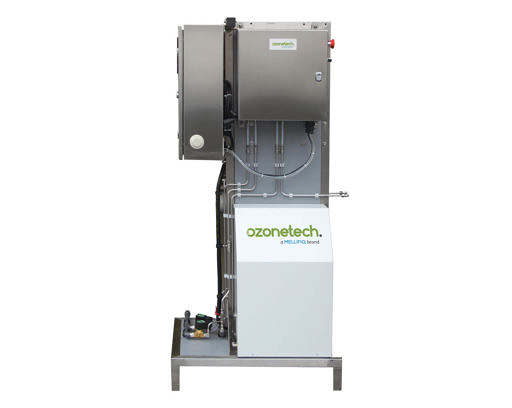